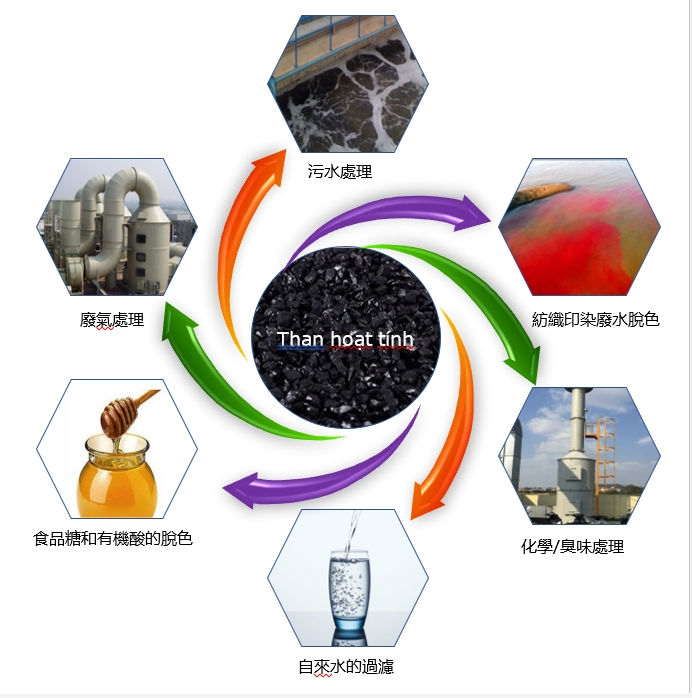
Textile printing and dyeing wastewater is a high-concentration wastewater containing a large amount of organic matter and pigments, which causes serious pollution and harm to the environment and human health. Traditional biological treatment methods are difficult to effectively remove these pollutants, so it is necessary to find more efficient, economical and environmentally friendly treatment technologies. Activated carbon is an adsorbent with high specific surface area and porous structure, which can adsorb organic matter and pigments in water, so as to achieve the purpose of purifying water quality. This article will introduce the effects and benefits of using activated carbon in textile printing and dyeing wastewater treatment, and provide some practical application cases.
Adsorption principle of activated carbon
Activated carbon is made of wood, fruit shell, coal and other organic matter after high-temperature roasting and activation under anoxic conditions. Its surface area can reach more than 1000 square meters per gram, and there are micropores and Mesopores form a huge adsorption space. When activated carbon is in contact with water, organic matter and pigments in the water will be adsorbed to the surface or internal pores of activated carbon due to intermolecular Van der Waals force, electrostatic force, hydrogen bond force, etc., thereby achieving water purification.
Adsorption effect of activated carbon
In textile printing and dyeing sewage treatment, activated carbon can effectively remove organic pollutants such as chroma, COD, BOD, ammonia nitrogen, phenols, aromatic compounds in water, and improve the transparency and biochemical degradability of water quality. According to different sewage characteristics and treatment requirements, different forms and specifications of activated carbon can be selected, such as powder activated carbon, granular activated carbon, fiber activated carbon, etc. Powdered activated carbon has the characteristics of large specific surface area, fast adsorption speed, and wide application range, but it needs to increase solid-liquid separation equipment and recycling equipment, otherwise it will cause secondary pollution and waste of resources. Granular activated carbon has the characteristics of stable structure, easy regeneration, and convenient operation, but requires a large contact time and high investment costs. Fiber activated carbon has the characteristics of high specific surface area, large adsorption capacity, and strong regeneration ability, but requires higher manufacturing technology and more expensive raw materials.
The use of activated carbon in textile printing and dyeing wastewater treatment has the following advantages:
- Environmental protection: Activated carbon is a natural, non-toxic and harmless substance that will not produce any by-products or residues, and will not cause secondary pollution to water quality or ecology.
- Economic: Activated carbon is relatively inexpensive to manufacture and can be regenerated by physical or chemical methods, extending its life and reducing its operating costs.
- Efficient: Activated carbon has a fast adsorption speed and a large adsorption capacity, which can remove various organic substances and pigments in water, and improve the standard and stability of water quality.
- Flexible: Activated carbon can be selected in different forms and specifications according to different sewage characteristics and treatment requirements, and combined with other treatment methods to achieve the best treatment effect.
The following are some actual cases of using activated carbon in textile printing and dyeing wastewater treatment:
- The COD of printing and dyeing wastewater from a textile factory is 800mg/L, and the chroma is 800 degrees. After biochemical treatment, the COD is reduced to 200mg/L, and the chroma is reduced to 200 degrees, which still cannot meet the discharge standard. The plant uses powdered activated carbon for advanced treatment, the dosage is 100mg/L, and the contact time is 30 minutes. The results show that the COD drops below 50mg/L and the chromaticity drops below 20 degrees, reaching the first-level emission standard.
- The COD of printing and dyeing sewage from a printing and dyeing factory is 1000mg/L, and the chroma is 1000 degrees. After biochemical treatment, the COD is reduced to 300mg/L, and the chroma is reduced to 300 degrees, which still cannot meet the discharge standard. The plant uses granular activated carbon for advanced treatment, the filling amount is 10kg/m3, and the empty bed contact time is 15 minutes. The results show that the COD drops below 80mg/L, and the chromaticity drops below 30 degrees, reaching the first-level emission standard.
- The COD of printing and dyeing sewage from a printing and dyeing factory is 1200mg/L, and the chroma is 1200 degrees. After biochemical treatment, the COD is reduced to 400mg/L, and the chroma is reduced to 400 degrees, which still cannot meet the discharge standard. The plant uses fiber activated carbon for advanced treatment, the filling amount is 5kg/m3, and the empty bed contact time is 10 minutes. The results show that the COD drops below 60mg/L, and the chromaticity drops below 10 degrees, reaching the first-level emission standard.
Conclusion
The use of activated carbon in the treatment of textile printing and dyeing wastewater is an efficient, economical and environmentally friendly technical method, which can effectively remove organic matter and pigments in water, and improve the standard and stability of water quality. According to different sewage characteristics and treatment requirements, different forms and specifications of activated carbon can be selected and combined with other treatment methods to achieve the best treatment effect.
Comments